Proprietary Technology
Our technology makes us stand out. A unique combination of polymer development (science) and proprietary process creates cleaning rollers which give the best cleaning, no reverse contamination, do not require high applied loads and can dissipate static. These products are the result of over 35 years of roller formulation and roller making process development.
Teknek’s adhesive products are the same, expertly engineered for contact cleaning applications. Our base materials are made to exacting specifications, the adhesive formulation is unique and our sheeting processes patented.
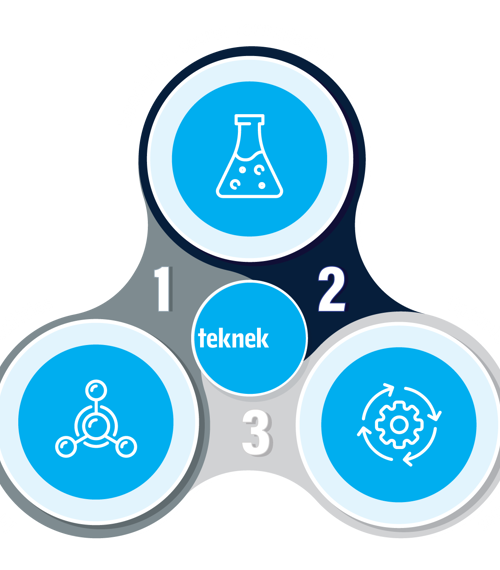
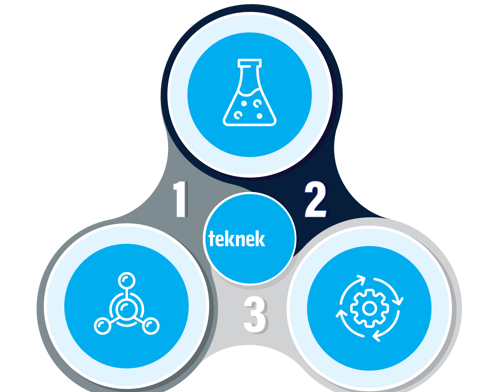
The unrivalled cleaning performance of our IP protected elastomer rollers is the result of three key components:
1) Specialist, secret formulations
2) In-house compounding facilities
3) Optimised production processes
honed and perfected in the context of more than three decades of in-depth application experience.
Contact Cleaning - A Simple Concept With Powerful Results
At Teknek, our cleaning concept is a simple one. However turning it into equipment that provides effective cleaning in a variety of applications is difficult. A deep understanding of customer processes and how to apply molecular science to achieve the best cleaning is key.
In principle, an elastomer cleaning roller makes contact with the surface to be cleaned. This roller picks up the particles of contamination and captures them on an adhesive roll. Permanently removing the particles ensures fewer defects in subsequent processes.
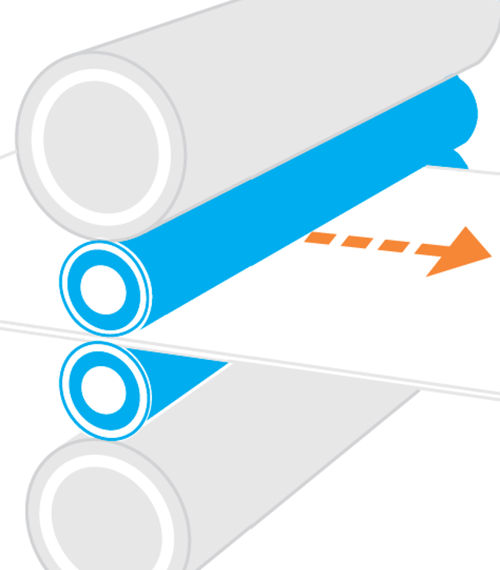
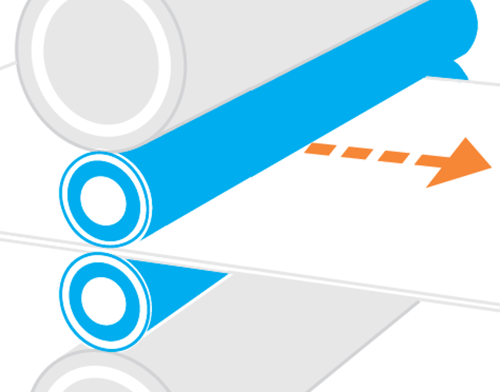
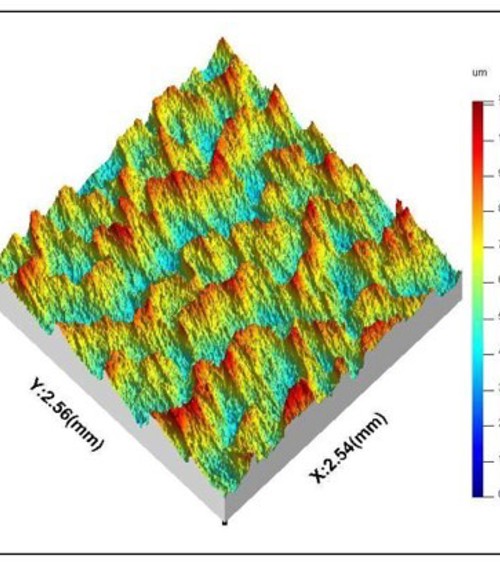
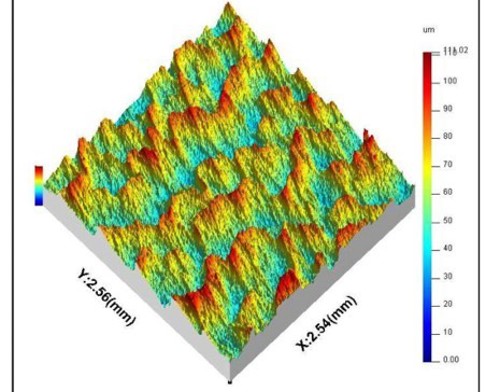
Remove particles ranging from several millimetres down to nanometer size
We understand the forces of adhesion that hold particles onto surfaces. So we can tailor the cleaning rollers and adhesive rolls to optimise their cleaning performance across many industrial applications.
We also respond to customer requirements with innovative elastomer roller and adhesive combinations. These allow our technology to remove a wide range of particle sizes, from several millimetres down to 10nm.
Teknek cleaning rollers can remove particles from substrates of many different materials – for example from 30 micron thin plastic film or 10mm thick sheets of glass. The technology works in many different operating environments, including high vacuum deposition on webs and ESD sensitive assembly areas in electronics.
Benefits and Limitations of Contact Cleaning
Contact cleaning is the preferred defect elimination technique when wanting to remove dry unattached particles from flat surfaces.
It is highly efficient for a wide range of particle types and sizes – sub micron to 5mm, metallic and non metallic, for example process contamination. Highly effective for most materials, it is used to clean metal foils, laminates, films, circuit boards, fine leathers and other high value materials.
Both sheets of materials and large roll to roll materials are well suited to contamination removal using this technique.
Applications which use materials which tend to shed high volumes of particles, for example clay coated card, fibreboard, non wovens are more suited to techniques such as high velocity vacuum systems which remove larger particles, or a hybrid system which combines a gross particle removal system with contact cleaning