Static charges in advanced production processes - Impacts & Mitigation
Across many sectors static charges negatively affect advanced production processes. For the electronics sector static charges result in high levels of defects and failing final products.
For some time, this Industry has developed companywide static control programs with perhaps the best known one being ANSI/ESD s20.20. This seeks to reduce defects and failures caused during the manufacturing process.
Within the Auto electronics sector this is a fundamental part of the zero defect/zero rework strategy. As the implications of both ESD and EOS events have become more widely understood, and at the same time electronics have become more susceptible to those static events attention has been focused on the Automatic Handling Equipment used in the production of both PCB’s and PCB assemblies.
Minituartistion, along with embedded components and new materials requires a low static production process, including the contamination removal equipment.
Static events are not only not well understood, but they are also unseen. Many rely on measuring the residual charge on a panel or board after it exist the process, for example as it leaves the cleaner. However, this does not represent the environment within the machine as most equipment makers fit an ionizing bar on the exit. So, whilst the residual charge at the external measuring point may well be 100 volts or lower, at the point whereby the cleaning roller touches the panel/board the local charge may well be greater than 20,000 volts. Any damage, particularly EOS damage, will not be detected until the product fails in the field, these particularly problematic failures are referred to as latent defects.
The static event damages the product, but it still operates at final test before shipping. However, it’s not long before the weakened product fails in the field.
Teknek Tek-BC-20: ANSI ESD s20.20 certified Low Static Cleaning System
Our Tek-BC20 board cleaners are third party certified to meet ANSI/ESD s20.20 giving Tier 1 producers complete peace of mind. The patented system is using static dissipative cleaning rollers and static dissipative adhesive rolls along with a special grounding system.
To date, Teknek machines are the only contact cleaning equipment third party approved to guarantee low static cleaning under ANSI /ESD s20.20.
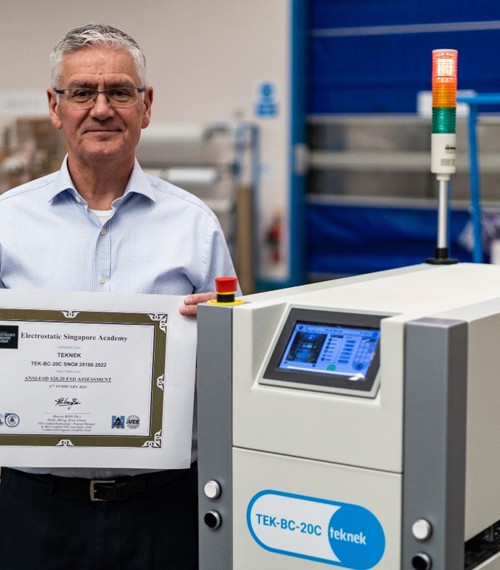
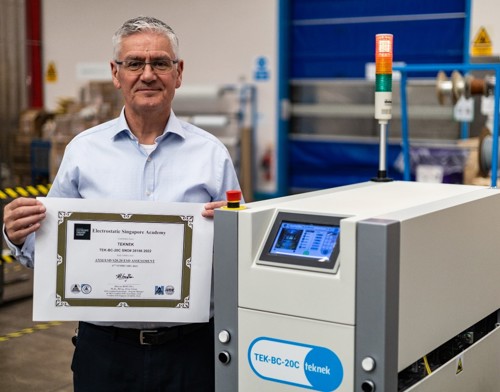
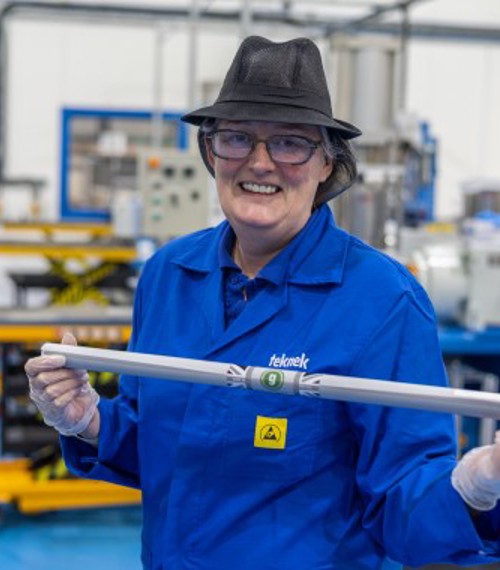
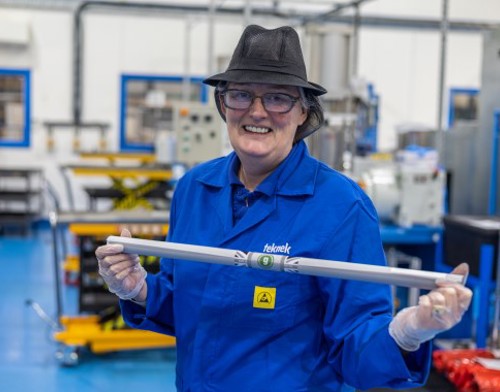
Anti-Static ≠ Static Dissipative
Despite well developed standards there remains much confusion as to what is required to achieve excellent contamination removal in a low static environment. Fortunately, the international standards provide clear guidance, thus:
Items which contact the substrate must be static dissipating. This is not to be confused with anti-static. Understanding this difference is vital to complying with the requisite standards. Only static dissipating cleaning rollers and adhesive rolls comply.
Anti-static helps to reduce charges but does not dissipate charge. Dissipating rollers ensure any charges are safely discharged to ground. Provided the system is grounded.
The key components of the cleaning system must be well grounded, in the case of this type of equipment ANSI/ESD s20.20 helps. Grounding to Clause 6.1 - <1MΩ is needed.